Data & Tools | Publications | Training |
What is it?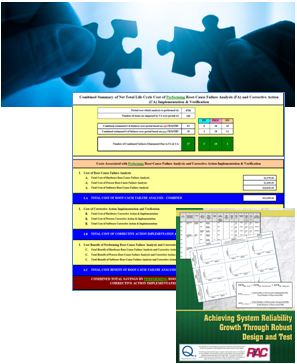
A root cause is the basic physical phenomena that results in a product/process “failure”. Root cause analysis (RCA) is a systematic approach for identifying and eliminating a root cause. A failure “symptom” will reoccur if its root cause is not eliminated, even if that “obvious” symptom looks like it was corrected. Reliability growth can occur only if root failure causes are identified and removed.
What’s the payoff?
A formal RCA process promotes reliability growth in products and processes. Up-front investment in strategic performance of RCA can result in significant savings in total life cycle cost. It can also promote a “lessons-learned” process for understanding failure relationships, causes, effects and solutions.
How can we help?
- Perform analyses to determine when RCA should be cost-effectively performed and quantify the long-term cost savings that result.
- Perform or participate in RCA to determine the true root cause of failure, as opposed to a failure symptom
- Identify a candidate corrective action (or actions) to ensure that a root failure cause (and not just a symptom) has been eliminated or suitably mitigated
- Collect and analyze data to verify that a corrective action has successfully resolved a root failure cause
- Define and implement a closed-loop reporting system/ database that includes RCA and corrective action results
Related Data & Tools:
Total Life Cycle Cost Benefits Calculator for Root Cause Failure Analysis Decision-MakingThe purpose of this Workbook is to estimate the net total life cycle cost (TLCC) impact of performing root cause failure analysis and corrective action (CA) identification, implementation and verification to improve system, product, assembly, component, part or process reliability.
Related Publications:
Practical Applications of the RIAC System Reliability ToolkitThe purpose of this publication is to provide illustrative examples of the more common mathematical calculations and statistical techniques utilized by reliability engineers in the practical performance of their daily activities. It is intended to be used as a companion to the RIAC “System Reliability Toolkit”, as the foundations of all of the techniques illustrated in this publication are discussed therein.
Reliability Modeling – The RIAC Guide to Reliability Prediction, Assessment and EstimationThe intent of this book is to provide guidance on modeling techniques that can be used to quantify the reliability of a product or system. In this context, reliability modeling is the process of constructing a mathematical model that is used to estimate the reliability characteristics of a product.
Achieving System Reliability Growth Through Robust Design and TestThis book offers new definitions of how failures can be characterized, and how those new definitions can be used to develop metrics that will quantify how effective a Design for Reliability (DFR) process is in (1) identifying failure modes and (2) mitigating their root failure causes.
Related Training:
Staff at the RMQSI Knowledge Center have provided many years of value-added consulting and training experience in the RMQ Engineering disciplines, to both commercial and government clients. Browse through our website to learn more and contact us to see how we can develop and present customized training to your organization.