Data & Tools | Publications | Training |
What is it?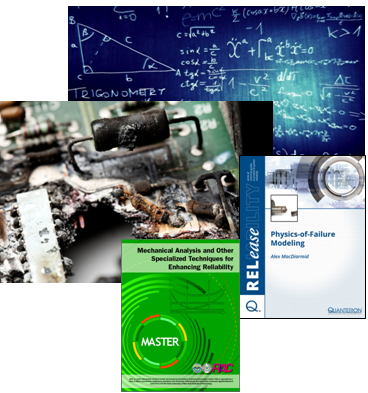
Reliability Physics is a technique for identifying and understanding the physical processes and mechanisms of failure. Currently, the terminology “Physics-of-Failure” (PoF) is widely used. It is synonymous with reliability physics.
What’s the payoff?
All materials, manufacturing and assembly processes can be characterized. Potential component level failure sites and mechanisms can be identified and their likelihood of occurrence quantified. Unacceptable failure modes/mechanisms can be proactively mitigated.
How can we help?
- Define a Reliability Program strategy that optimizes the advantages of PoF approaches within available resources
- Assist in the definition, selection and use of appropriate materials, parts and design configurations that meet the characteristics and physical stresses of the environment
- Identify or tailor existing relevant PoF models, or develop customized new models, that characterize component, product or system life
- Perform analyses and formulate simulations/tests that address the predominant failure modes/mechanisms of existing or future designs/processes
- Provide training on how to model, predict, collect/analyze data and apply other PoF-based techniques to benefit your specific products, processes and applications
Related Data & Tools:
Staff at the RMQSI Knowledge Center have provided many years of value-added consulting and software/tool development experience in the RMQ Engineering disciplines, to both commercial and government clients. Browse through our website to learn more and contact us to see how we can develop software and tools tailored to the specific RMQ needs of your organization.
Related Publications:
GaAs MMIC Reliability – High Temperature BehaviorThe gallium arsenide monolithic microwave integrated circuit (MMIC) is a developing circuit technology which plays a key role in both military and commercial microwave systems. Due to the required high power dissipation, the microwave monolithic technology must operate in temperatures in excess of 150°C and often above 200°C.
Photonics Materials, Devices and ReliabilityThis publication presents photonics in the context of reliability. Design concepts are presented to promote material combinations that are robust and reliable. All wearout mechanisms must be understood, as well as their effect on performance. Metalizations and their degradation mechanisms must also be understood. This book highlights their contribution to overall photonic material and device reliability.
Reliability of Compound Semiconductor Analogue Integrated CircuitsMaterial scientists, device technologists, and microwave designers must focus on the reliability concerns of the products which are being developed from compound semiconductor structures. The book focuses on a physics of failure approach to the understanding of MMIC reliability, covering basic failure modes for each of the device building blocks, up to packaged MMIC modules.
Reliability of High Temperature ElectronicsStandard electronic devices are based on military-type semiconductors which are rated for 125°C. Without cooling, engine-located electronics in many applications can face operating temperatures between -55°C and +200°C. Thus, the development of appropriate 200°C and higher semiconductor devices will make it necessary to utilize air or liquid as the cooling medium.
Reliability and Quality in Microelectronic ManufacturingThe manufacture of microcircuits begins with the silicon or gallium arsenide wafer and, after several processing operations, results in a fully packaged electronic component. For semiconductor manufacturing, the processing operations allow the industry to design-in reliability through the proper selection of materials, processing parameters, and technologies. The student of manufacturing must therefore be taught the critical relationships between manufacturing, reliability, and quality.
Reliability Modeling – The RIAC Guide to Reliability Prediction, Assessment and EstimationThe intent of this book is to provide guidance on modeling techniques that can be used to quantify the reliability of a product or system. In this context, reliability modeling is the process of constructing a mathematical model that is used to estimate the reliability characteristics of a product.
Mechanical Analysis and Other Specialized Techniques for Enhancing Reliability (MASTER)This document is specifically targeted to address this problem, outlining the competing approaches to part reliability predictions, including Statistical Analysis of relevant failure data, Physics of Failure modeling, Empirical Failure Models and Data, and other less common but acceptable methods.
Physics-of-Failure ModelingThe traditional approach to product reliability has largely been based on the statistical analysis of an item’s failure data. Analysts would predict the probability of a part/system failure from the percentage of times that an item failed either during testing or from historical use in the field. Eventually, statistical distributions were fit to an item’s time-to-failure data, allowing for the estimation of more informative reliability characteristics (e.g., characteristic life, rate of failure, etc.).
Interference Stress/Strength AnalysisIn simplest terms, an item fails when a stress to which it is subjected exceeds the corresponding strength. In this sense, strength can be viewed as “resistance to failure”. Good design practice is such that the strength is always greater than the expected stress. The safety factor “η” can be defined in terms of strength… Read More
Which Variables Are Critical to Field Reliability? Design of Experiments (DOE) Can Help Optimize Your DesignEngineers are often faced with the problem of optimizing a process that includes a number of input variables. It could be an analysis of a manufacturing process, or even an analysis of a business process. They’re often challenged to find ways to reduce
Which Design is More Reliable? Weibull Provides Answers!Weibull Analysis is often used to analyze field or test failure data to understand how items are failing and what specific underlying failure distribution is being followed by failures that occur. One of our staff engineers was recently responsible for making a vendor recommendation for a limited life item that had a specified 5% minimum… Read More